Oil and Gas
The world’s first oil refinery was established in Ploiesti, Romania, 1856. As the new industry grew across the globe, the need for fire protection was identified, and in the 1920’s more mature refineries in US and Europe were being constructed. The first Passive Fire Protection (PFP) material used to protect structural steel potentially exposed to hydrocarbon fires was concrete. Since then, PFP has evolved and in the 1970’s epoxy intumescent fire protection was introduced for structural steel.
For Critical Process Control Equipment (CPCE), the first method of fire protection was stainless steel enclosures which protected the actuators and controls against hydrocarbon fire, however, especially for big actuators these were very large and heavy Stainless boxes that needed additional framing and support and extensive on-site work to install them. It was Thermal Designs in October 1985 that started the process of directly bonding passive fire protection for Critical Process Control Equipment (CPCE). Subsequently finding that all the current intumescent epoxies available on the market were not well suited for this purpose, our chemists developed a new product, which was released in the December of 1991, the introduction of
K-MASS. Since then K-MASS has evolved to Version 3, a higher performing and easier to mold product that became our customers preferred fireproofing choice for CPCE.
K-MASS and our associated products are designed, developed and formulated as a PFP for CPCE exposed to hydrocarbon fires. Over the years, it has become the preferred choice of passive fire protection based on performance. K-MASS provides superior insulation characteristics in High Heat Flux (HHF) and rapid temperature rise hydrocarbon fires by maintaining cooler surface temperatures and lower heat transfer rates. By being directly bonded to the substrate, K-MASS protects without compromise.
-
Fully tested under UL 1709 as per API 2218
-
Functional system (PFP+ Actuator) 3rd party witnessed tests under UL 1709 fire conditions
-
Provides minimum of 30 minutes protection for CPCE exposed in 1,093°C (2,000°F) hydrocarbon fires
-
All the original actuator design features are kept intact
-
Permanently and directly bonded to the CPCE parts, does not promote CUI
-
Provides complete access to all actuator parts, without the need of any special tools
-
The fireproofing cannot be left out in case of maintenance, as it’s directly bonded to the CPCE
-
Minimum space required
-
No additional installation cost on-site
-
It is a durable and weatherproof solution
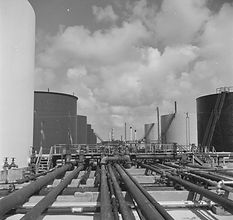
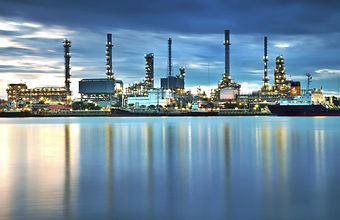
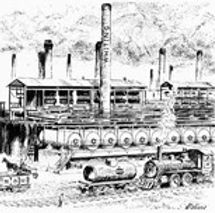